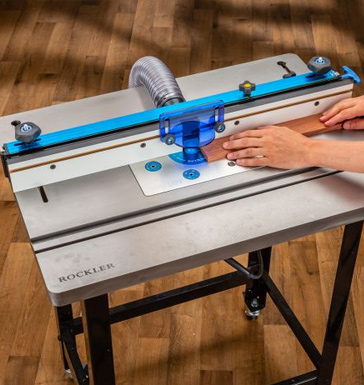
There are many angles you should consider when cutting crown molding. These angles include spring, miter, or diagonal. The key to a fitting fit is knowing which angle to use. Here are some tips and tricks to measure the angles for your crown molding.
Cut a miter angle
A power saw is the best way to cut miter angles for crown molding. Set the saw at 45 degrees to the left or right when preparing a miter angle. Next, measure the length of crown molding from one corner. If you are unsure about the exact length, slide the test block under your crown to confirm. A measuring tape can be used to ensure the crown molding will fit.
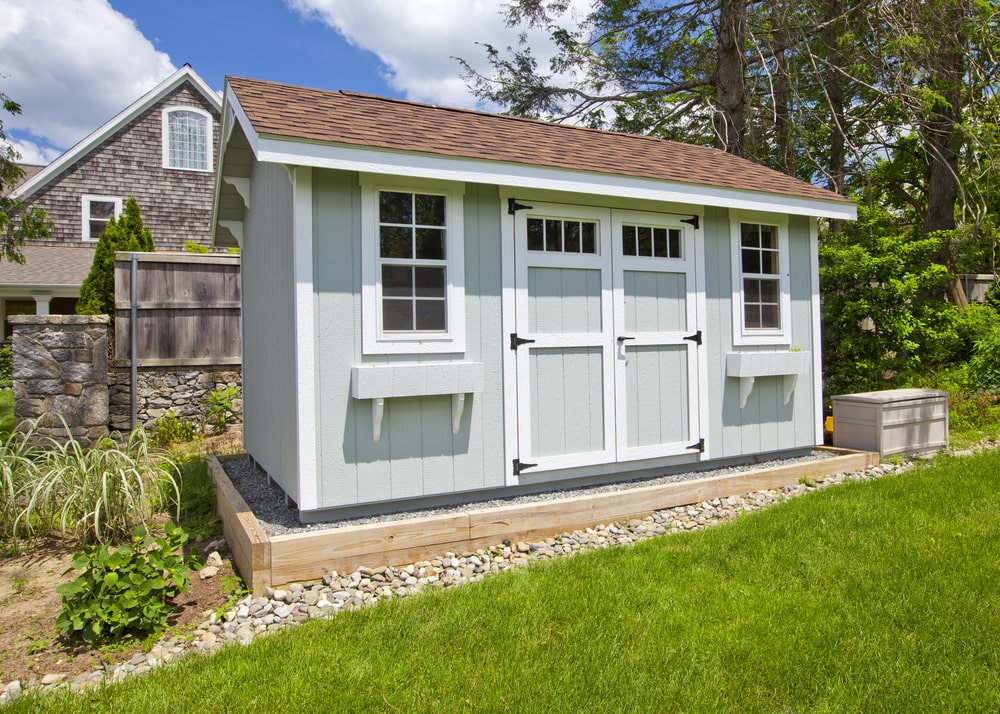
Create a bevel angle
To properly install crown molding, it is essential to understand the angles. Crown molding is standardized in most cases so the angles can be easily determined. However, there are a few factors to take into account when cutting bevel angles. The spring angle refers to the angle between the molding's back and the wall after it is installed. You can find a chart with these angles.
You can cut a diagonal angle
You will first need to lay the crown molding flat onto your saw table. Next, make a diagonal cut approximately one-half an inch from one end. Keep going until you've completed the entire loaf. You will then need to cut another diagonal angle that is approximately the same size as the original one. Next, attach the crown molding and backer board with a nail gun. This step is crucial and takes patience.
Calculate a spring angle
For crown molding to be calculated, it is necessary that you know the wall's width. You can also check the angle by using a measuring tape. The angle between the back and wall of the crown when it is being installed is called a spring angle. Crown molding usually has a 45deg to 52deg angle. A test block is also available to determine the angle for the spring.
Make a miter join
To make a miter joint in crown molding, follow these steps: - Place the piece of molding on the table. - Turn the miter base to the left. - Place your right side of the piece onto the table. - Make a right angle with the piece. - Make sure to save the right end of your cut. - Turn the blade to its maximum speed. Keep a firm grip. - Make sure that the blade is not in direct contact with the mold.
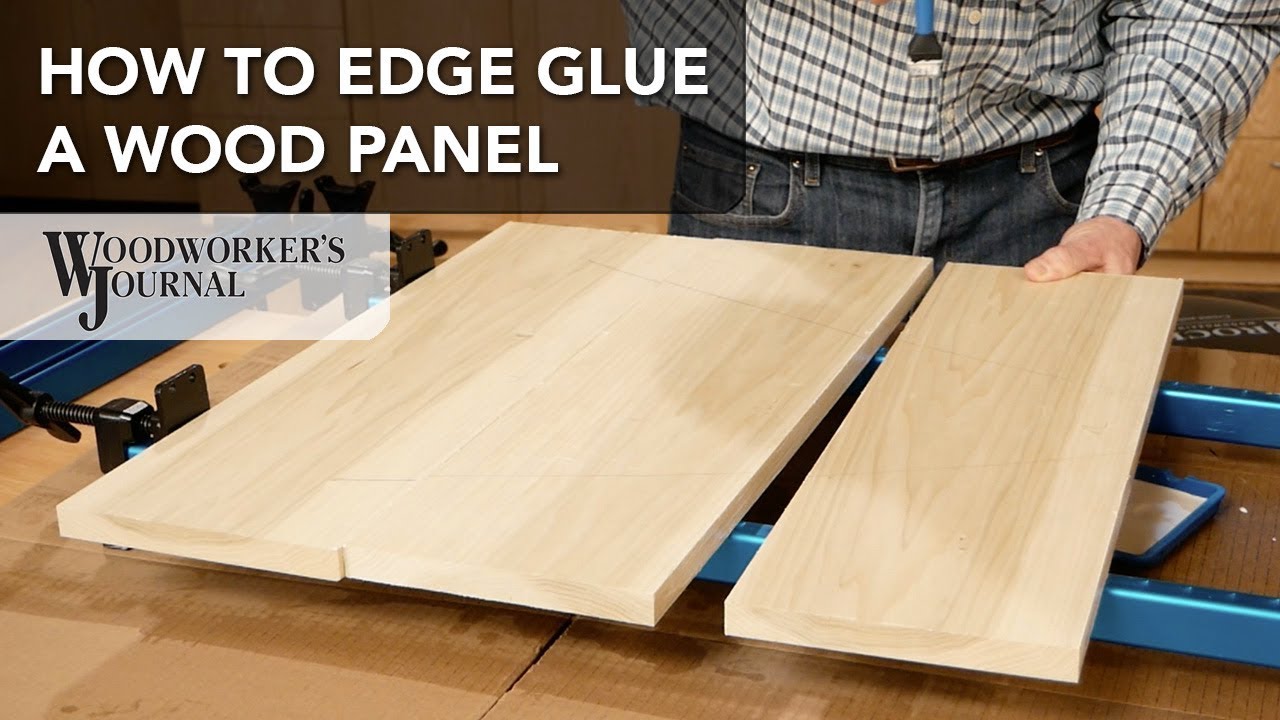
Keep spring angles consistent
A finder or angle chart is required to ensure the crown molding's spring angles are consistent. An angle chart indicates the angles between your crown's back, and the wall on which it will be placed. The most common angles crown moldings come with are 45deg/45deg as well 52deg/38deg. If you don't have an angle chart, you can always slide a test block underneath the crown.
FAQ
Which woods are good to use for furniture-making?
Woods are classified according their hardness. Softwoods are pine, cedar and cypress. Because they are resistant, they can be used for outdoor furniture. You can find hardwoods like oak, maple, mahogany, teak, and others. They can't withstand the elements outside so they're best kept indoors.
Do I have the potential to make a decent living doing this?
Yes! Many woodworkers have this ability. According to the U.S. Bureau of Labor Statistics, the median annual woodworker wage was $34,000 in May 2012. This is more than the national average of 31,000 per annum.
How can I learn basic woodworking skills
A great way to start learning how to build furniture is by building a simple bench for yourself. This project can be completed with whatever wood you have available at home. If you don't know what kind of wood to use, then go ahead and buy some cheap pine boards from Home Depot or Lowes. After building your bench, sand off any rough edges and apply a stain or varnish.
Statistics
- Overall employment of woodworkers is projected to grow 8 percent from 2020 to 2030, about as fast as the average for all occupations. (bls.gov)
- In 2014, there were just over 237,000 jobs for all woodworkers, with other wood product manufacturing employing 23 percent; wood kitchen cabinets and countertop manufacturing employing 21 percent. (theartcareerproject.com)
- If your lumber isn't as dry as you would like when you purchase it (over 22% in Glen Huey's opinion…probably over 10-15% in my opinion), then it's a good idea to let it acclimate to your workshop for a couple of weeks. (woodandshop.com)
- The U.S. Bureau of Labor Statistics (BLS) estimates that the number of jobs for woodworkers will decline by 4% between 2019 and 2029. (indeed.com)
External Links
How To
How to join two pieces of wood together without nails
Many people love woodworking. You can make useful items from wood with your hands, which is both relaxing and fun. You might want to join two pieces from the same wood, but you don't need to use nails. This article will demonstrate how to do so to preserve the beauty of your woodwork.
Before you can join the wood pieces together, you need to remove any rough edges. Sharp corners can cause problems down the line. Now you can start gluing the boards together.
If you are working with hardwood, only one side should be glue. Use glue on both the sides for softwoods, such as cedar or pine. Once the glue has dried, press the boards together until they are fully adhered. Before you proceed to the next step, be sure to let the glue dry completely.
After you've glued your boards, you'll want to drill holes into the joints where you plan to insert screws. The size of these holes depends on what type of screw you choose to use. If you are going to use a half-inch wood screw, you will need to drill at least 3/4 inch deep.
After drilling your holes, drive the screws into the board's backside. You should be careful not to touch the board's front surface. This could cause damage. Try to not hit the ends of the screws when driving the screws. This will prevent splitting in the end grain of the wood.
After your project is completed, you will need to protect it from the weather. To do this, you can seal the entire furniture piece or just cover the top. You'll want a product that lasts for many years. You can choose from oil-based varnishes or polyurethane, shellac and lacquer as examples.
These products can usually be found at any home improvement store. Make sure you get the right product for your job. Don't forget to keep in mind that some finishes are toxic. Protective gear should always be worn when handling these finishes.