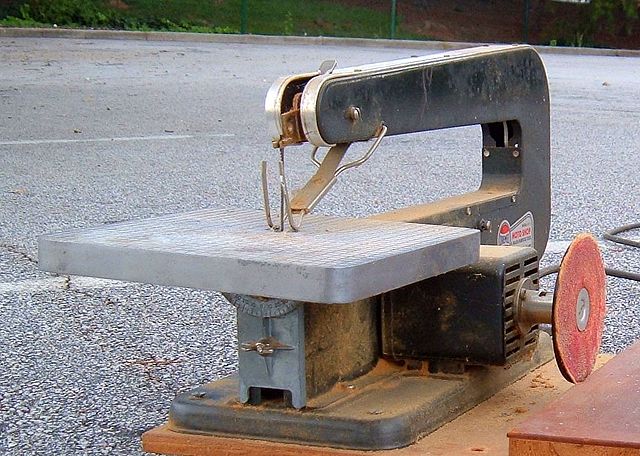
This guide will show you how to make intarsia wood art. The information presented here covers Wood types, Patterns, Tools, and Techniques. This exciting craft is described in detail below. Depending on your skills, you might also consider using a different kind of wood. To get an idea of the process, you can make a sample piece if you are new to the craft.
Patterns
You can make intarsia ornaments for holiday, Christmas, and tree occasions if you're a good woodworker. The book's intarsia wood pattern pages are suitable for all levels of experience and demonstrate the artistic nature of the process. There are a total of 21 full-size intarsia patterns included, with helpful information on blades, wood, and shaping.
Intarsia allows you to create an original piece of furniture, or wall hangings by using different wood species. It's similar to building a puzzle using different wood pieces placed in close proximity. The wood is then stained or polished and each piece is then assembled to give the project depth and character. It can be difficult to create intarsia wood patterns. To make the best decisions about your project, you will need to find a reliable source of free intarsia designs.
Tools
Special tools are required to create intarsia that is beautiful. A small belt-sander is a great tool to quickly remove material from the surface and smoothen out edges. A dremel and flex shaft are useful tools to shape or sand small details. These tools come with different blades, and are useful for small areas shaping or sanding.
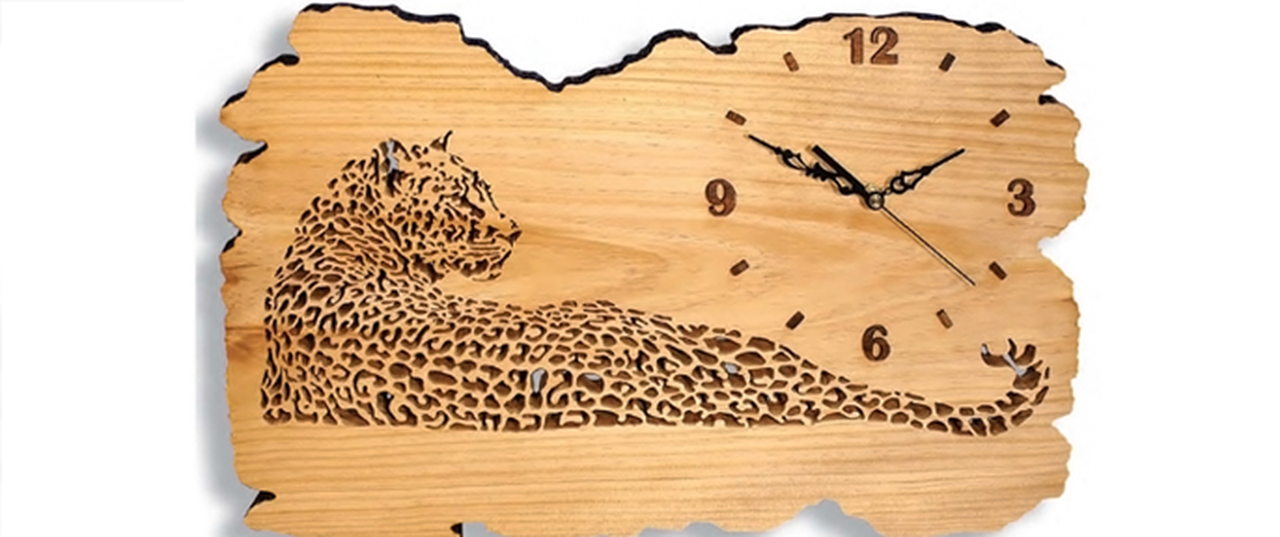
Jigsaw: Jigsaws can be used to cut wood but not in the same way as a scrollsaw. Sanders are required to smoothen wood surfaces. Intarsia woodworking requires two different types of wood that contrast in color and grain. The wood will then need to be stained differently. After the wood has been cut, it is sanded to form a mosaic-like pattern.
Techniques
It is easy to create stunning intarsia pieces if you use the correct techniques. A pattern can serve as a starting point for artistic creativity. You'll be well on the way to creating stunning pieces of intarsia wooden art with these ideas. These are some of the techniques you can use:
Select the project design. Make duplicates of your pattern. Next, pick the wood species you will use. Different wood species can have different properties. Roughing out the thickness of each piece of wood gives your project a more interesting depth and dimension. You can also add pieces by glueing on additional layers of wooden. Finish your project by removing any backing material and leaving the intarsia piece as it is.
Woods to use
Whether you're a beginner or have been working with inlaid wood for years, this new book will give you the tools and techniques to make beautiful pieces that stand out. Kathy's progressive teaching style will help you learn everything, from the basics to the subtleties of color breaks. You'll be referring to this book even if you have never made intarsia before.
First, select woods that will complement each other and have the same grain orientation. To make a teddy, 20 pieces of wood must be made from four different kinds of wood. Each grain has a slightly different texture. This will require a saw with high speed blades. Once you've identified the wood's colors and grain orientation, it is time to cut and stain.
Colors
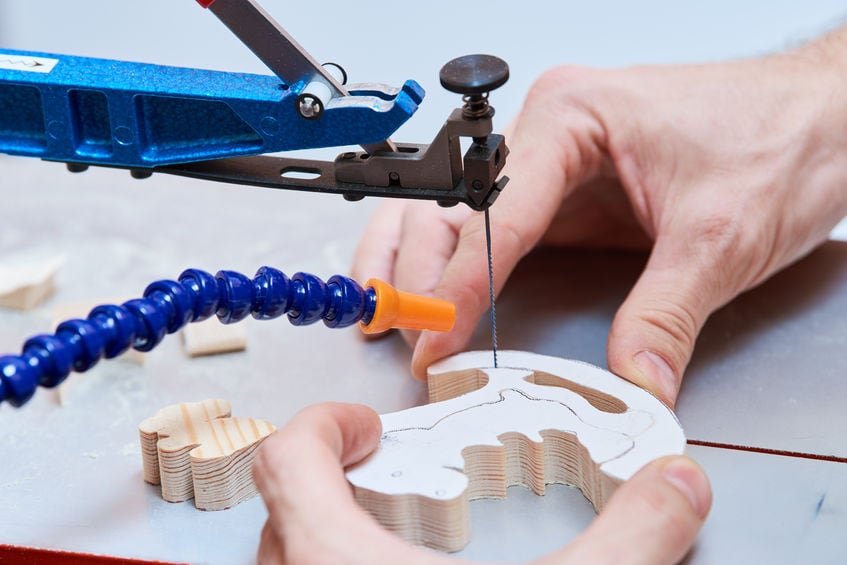
The intarsia pieces come in a wide range of colors. While saps and heartwoods are either reddish brown or grey black, they are both white. Cherry is one example of a wood that darkens with age. Cherry has a light to medium tone at first and then becomes darker with age when exposed to sunlight. Cedar and other woods can have different tones within a board. This gives your project depth.
Intarsia refers to a type art made by joining different pieces of wood together and creating patterns. Although it originated in the Islamic world and is now associated with Italy, it has been a popular art form for many years. Woodworkers create a three-dimensional illusion by using different wood colors with varying thicknesses. Intarsia can be found on jewelry boxes or wooden chests.
Time-consuming process
Intarsia is a complicated process that requires the use of various types of wood and staining techniques. Artists must have a variety of wood types and stain colors in order to create beautiful intarsia designs. Although plywood and Birch are the most popular types of wood, other types of wood are suitable. Artists choose the wood they prefer, but it all depends on their individual preferences. For intarsia projects, many craftsmen prefer Western Red Cedar.
Intarsia woodworking starts with cutting and labeling the inlay. The artist then glues the pieces together. After the glue dries, the woodworker finishes off the piece using a double bevel edge inlay. This time-consuming process requires a great deal of skill, and the finished product is truly a work of art.
FAQ
What should a woodworker be paid per hour?
The hourly rate of a professional woodworker depends on many factors including experience, skill level, availability, location, etc.
The hourly average rate for skilled woodworkers runs between $20-$50.
A less skilled woodworker might charge as low as $10 per hour.
Is it possible to learn woodworking by yourself?
Doing is the best way to learn any subject. Woodworking takes practice, skill, patience and experience. Every craft takes practice and patience.
It is the best way to learn to do something is to actually do it. Start small and then build upon what you've learned.
What's the time taken to finish a piece furniture?
It depends on the size of the piece of furniture. A smaller project like picture frames or boxes can be completed in a single day. Larger projects such as tables and desks can take several days to complete. It takes time and effort to properly stain the wood.
What tools do I need to start as a woodworker and what should I learn?
Woodworking takes practice and patience. It takes time to learn how to use all the different tools and techniques required for woodworking.
There are many kinds of woodworking equipment currently on the marketplace. Some people prefer to use power tools while others prefer manual tools.
Your choice, however, is up to you. However, you need to ensure that the tool you use is the right one for the job. A basic set of hand tools may be enough for you if your skills are not yet developed.
You could also try learning how to use a router which is used to cut intricate shapes into wood. These are available at most hardware stores.
Do you have any advice on how to start a woodworking business.
It can be difficult to start a woodworking shop. But if you're passionate about your hobby, you won't mind putting in the effort. You might even enjoy running your own business.
When you are launching a new venture, it is important to be aware of the possibility that you will encounter unexpected difficulties. You might run out unexpectedly of funds. Maybe customers won't be willing to pay what you want. You need to be ready for these situations if you want to survive.
A good tip is to open a separate bank account for your business. You'll be able to track how much money comes in and out.
Statistics
- In 2014, there were just over 237,000 jobs for all woodworkers, with other wood product manufacturing employing 23 percent; wood kitchen cabinets and countertop manufacturing employing 21 percent. (theartcareerproject.com)
- Most woodworkers agree that lumber moisture needs to be under 10% for building furniture. (woodandshop.com)
- If your lumber isn't as dry as you would like when you purchase it (over 22% in Glen Huey's opinion…probably over 10-15% in my opinion), then it's a good idea to let it acclimate to your workshop for a couple of weeks. (woodandshop.com)
- The best-paid 10 percent make $76,000, while the lowest-paid 10 percent make $34,000. (zippia.com)
External Links
How To
How to make wood joints
This tutorial will help you join two pieces of wooden together. We will use the "pockethole joint," which means that we drill holes in the wooden pieces and then glue them together. If your wood has a straight grain, smooth surface, you can use this method. Dowel joinery might be a better option if your wood is not straight or flat. These are the steps
-
Drill Pocket Hole Joints. Start by measuring and marking the spot where the pocket hole joint will be placed. Then drill 3/4 inch deep holes into the ends of each piece of wood using a jig saw or handheld drilling machine.
-
Sand Smooth. Sanding the edges of the wood will help to prevent the joint from splitting later.
-
Glue both sides together. Apply glue to both ends of the wood. Allow the wood to rest for five minutes before clamping it together.
-
Attach the Pieces together. After the glue has dried thoroughly, secure the pieces so that they are flush.
-
Trim Joinery. After the glue dries completely, trim off any excess wood around the joint.
You should leave enough space between the pieces to allow you to turn them inside-out.