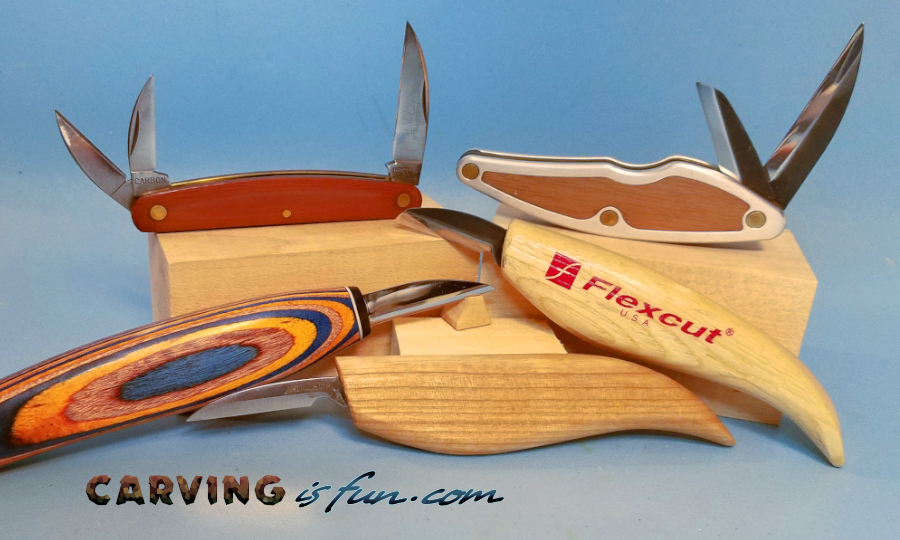
You should consider a few things when you are looking for an Oar Carving Knife. Size, sharpness, stag bone, lamination, and origins are all things to consider when you're purchasing your knife. This article will help you choose the best knife for your needs. This article will provide you with a guideline for choosing the right oar carving knife.
Size
Oar Carver's series of pocket knives for carving is a classic example of this art. Three sizes are available in the current lineup. Version 2 is bigger and has a thinner blade. Version 3 comes in a slightly larger size with a thicker knife and a wider space between them. Here are some tips on choosing the right size.
Sharpness
One of the most important aspects of any oar carving knife is the sharpness of its edge. Your edge will show signs wear such as chips, dullness or nicks. So it is essential to have a sharp knife. Luckily, it is relatively easy to gauge the sharpness of an oar carving knife by observing the edge. You can match the edge of each knife to its center with a magic marker.
One way to test the sharpness of an oar carving knife is to cut a piece of basswood across its end grain. The blade should cut through the wood with no drag marks or ripples. A smooth cut can be described as slicing through a baby’s bottom without leaving any marks. If you see any of these marks on the blade, it might not be sharp enough to use for carving. It is vital to ensure that the sharpness, or oar carving knives, are checked regularly.
Laminated blades
The Oar Carver series has been the most popular example of a pocket knife for carving. It was designed by Ross Oar who is also a world-renowned carver. Versions 1, 2, and 3 are the current versions. Each version is very different from the last. Version 2 has a wider gap between the blades. It also has a shorter edge. See the Oar Carpenter blade guide for more information.
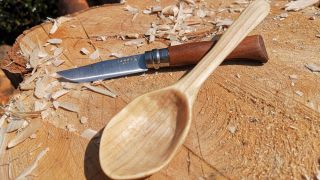
Mora makes two versions, the 106 and the 120. Both models have a laminated stainless steel blade. However, the Mora knife is slightly longer. Both knives have a basic oval handle, and are also sold with a snap sheath. Another model, the Mora Frost 122 has a laminated steel blade and a 61 Rockwell high hardness. This knife is great for carving and is durable and sharp.
Origins
The oar carving knife was created in Japan from ancient times. The handle is four-and-a-half inches long, and it is made of solid hardwood. The oar has a long, flat blade, with a flat tip. The blade of the knife measures 53 inches. The handle is made from a narrow, slender circle. The shaft and blade are separated by a thin slice of wood.
The earliest known carving tool is the oar, but its history runs much deeper. The oar was first used to transport people along the coast and riverine. Because it was easy to recognize and widely used, Admiralty chose the emblem oar. Other meanings might have been given to the oar, however. Listed below are some of its origins. If you are interested in learning more about the history and evolution of knife-making, they are also worth looking at.
FAQ
Is there a way to start my own woodworking company?
It is difficult to start your own woodworking company. There are many laws and regulations you need to be aware of. It doesn't mean that you have to go through the entire process of starting a business. Many people opt to join existing businesses instead. This way, you only need to pay membership fees and taxes.
What amount of money do I need to get started with my business?
Because each project is unique there are no exact numbers. These are the factors that will give you an idea of how much you'll need.
-
Materials cost
-
Tools and equipment
-
Time spent on the Project
-
Hourly rate
-
What amount of profit can you expect to make?
-
You can hire help, regardless of whether you have a plan.
For those just beginning, it may be a good idea to start small with simple items like boxes and picture frames. As you gain experience, you'll be able to tackle more complex projects.
What else should I know about woodworking in general?
It is easy to underestimate how much work it takes to make furniture. The hardest part of the process is actually finding the right wood. It is difficult to choose between the various types of wood.
A problem is that wood doesn't have the same properties. Wooden can split or crack, while some woods may warp. These things should be considered before you buy wood.
Statistics
- Average lumber prices rose about 600 percent between April 2020 and May 2021. (familyhandyman.com)
- The best-paid 10 percent make $76,000, while the lowest-paid 10 percent make $34,000. (zippia.com)
- Most woodworkers agree that lumber moisture needs to be under 10% for building furniture. (woodandshop.com)
- Woodworkers on the lower end of that spectrum, the bottom 10% to be exact, make roughly $24,000 a year, while the top 10% makes $108,000. (zippia.com)
External Links
How To
Here are some tips on how to drive nails in wood
It is essential to pick the right size and style of hammer before you can drive a nail in wood. The most common types of hammers are claw hammers, sledgehammers, mallets, ball peen hammers, and hatchets. Each kind of hammer has its own advantages and disadvantages. For example, a claw hammer works best when you want to hit something hard, like nails; however, it's difficult to control precisely where the blow lands. The sledgehammer works well for large areas, but is too heavy for smaller tasks.
After choosing the right hammer, place your hand flat against the side of the head so that the handle rests comfortably in your palm. Take the handle and hold it with both hands. But don't press down so hard you injure yourself. Hold the hammer straight up, keeping your wrist relaxed. You should then swing the hammer straight up, keeping your wrist relaxed. You should feel the impact of your hammer hitting the nail. Try practicing with a block to help you master the art of swinging a stick.
You can now drive the nail by holding the hammer to your body. You will need to position the nail so it is parallel to the wood. Keep your focus on the tip of each nail. Then, swing the hammer forward. Next, follow the motion of your hammerhead. Keep doing this until you are comfortable with the swing. Once you have mastered this technique, increase the power of your swings. To make it more powerful, hold the hammer up high to your shoulder and then bring it down. This will allow you to exert more energy.
Once you've made the first nail hole, take out the hammer. To pull out the remaining nails, use a screwdriver or pry bar. To avoid splitting the wood, make sure the nail heads are not touching the board's surface.